July 10, 2025
How a “Can Do” Culture Contributes to SIF Prevention: A Perspective from the Utilities Sector
Over the last 5 years, I’ve had the pleasure of working with amazing organizations in the Utilities sector. I’ve interacted with some of the most hard-working people there are – especially during storm restoration – who work tirelessly in all kinds of weather conditions to get the power back on. Although you might think that most utility worker injuries occur during storm restoration work, they do not. Like so many other industries, both Serious and Fatal injuries (SIF’s) and non-SIF’s tend to be more frequent during non-storm periods – often during what is described as routine work in the best of weather conditions. How can that be?
Utility Line Worker Crew Culture
To better understand this phenomenon, it’s helpful to better understand the common cultural characteristics of most line worker crews. These crews are often made up of 4-5 crew members with a crew foreman present nearly all the time. They have some great capabilities and characteristics:
- Prideful – mission driven to keep the lights on no matter the conditions.
- Strong ‘brotherly’ bonds – often self-contained (what happens in the crew, stays in the crew).
- Technically competent (highly skilled craft).
- Possess critical thinking skills to diagnose trouble and respond.
- Can do attitude – they get “stuff” done.
- Typically, hyper focused on the highest risk work and doing it safely. Much of the “other” work is not often considered work.
- Believe that zero injuries is not possible – “we work in a dangerous industry and stuff happens”.
From “Can Do” to “Make Do”
These strengths combine into what I’ll refer to as a “Can Do” approach to the work. Organizational leadership is often very appreciative that most of their workforce has this approach. That is, until some of these strengths are over-used and the approach moves from “Can Do” to “Make Do”. To better understand why this happens, it is helpful to learn what some of the influences on a line work crew are.
An Illustration
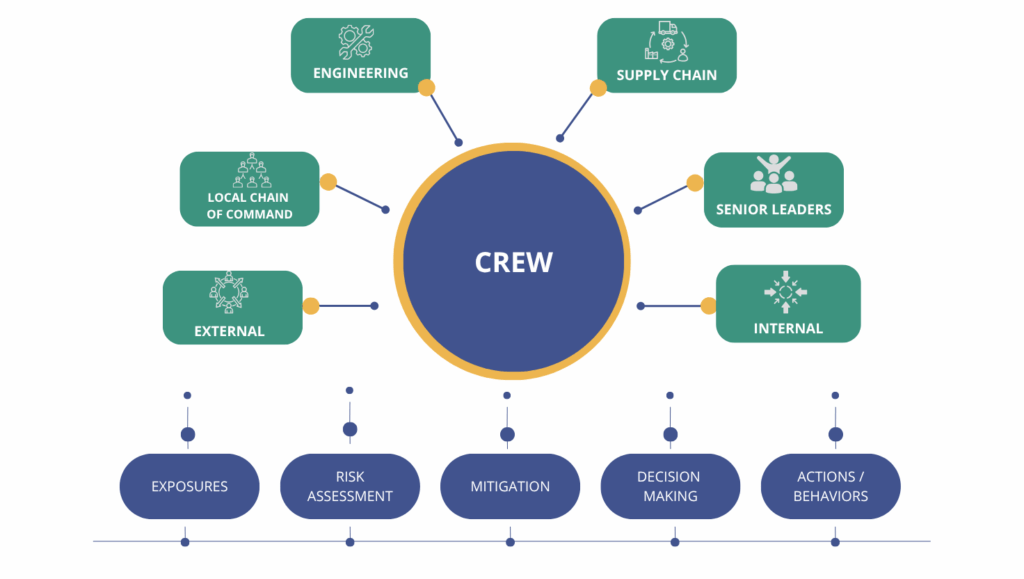
The bottom of this graphic illustrates the steps crew members go through each day that are intended to lead to a safe and productive day. There are several “influences” on how well these steps are performed.
- External – Today, electric customers are far more demanding of utility services. Although many understand power outages are a reality, they expect real-time information on when they can expect power to be restored. It is no longer a rarity for customers to approach a line crew with these kinds of questions.
- Local Chain of Command – The days often start with a briefing about the work to be completed. The best crews operationalize the approach for the day even before they leave the yard for the job. However, often the assigned jobs have unknown problems only to be learned once at the job site. When this occurs, it is often the most common catalyst to going from “can do” to “make do” – even when we don’t have the right equipment, tools, or materials to do the job in the safest way.
- Engineering – Even when the day’s job packets seem complete, they sometimes are not. The project site maps have not been updated, or the site’s other utilities haven’t been marked (or marked incorrectly) which further frustrates the crew and drives a “make do” approach.
- Supply Chain – The availability of the right equipment, tools, PPE, and materials relies on a strongly managed supply chain. These gaps in reliability are a significant contributor to crew distraction and frustration – further influencing the “make do” approach to getting things done.
- Senior Leaders – Most organizational decision making happens several layers above the crew level and has a significant implication on the safety of the crew. Project planning, staffing, safety rule/policy development decisions, and many others are significant drivers of crew satisfaction and engagement. The single most common driver of crew frustration with organizational decision making is that it is often communicated without “the why” – the underlying reason(s) for the new policy, rule, or procedure.
- Internal – Crew members bring their own “distractions” each day. Inside the crew, there are likely differences in how well crew members understand, assess, and mitigate risk. Further, based on how long they’ve been doing the work, they often have a too high tolerance of risk, even if it is understood. They also bring along their “outside work” distractions, such as problems they may be having with family relationships.
What can be done to improve safety results?
There are several steps you can take to drive safety improvement:
- Get visibility into these influences and seeing firsthand how they are impacting crew performance is the best way to drive improvement. It is important for leaders at all levels above crew foreperson to regularly get out in the field and observe these influences in real time. When “distractions” and “frustrations” are uncovered, look at those as a “gift” and commit to working to reduce or eliminate them. In addition, regular crew observations often reveals if the risk tolerance is too high.
- Ensure crew members are skilled at hazard identification and how to mitigate the risks. Teach crew members to watch specifically for the catalysts that lead from “can do” to “make do” and encourage those situations to be where they use stop work authority.
- Improve work design to ensure the crew foreperson can spend nearly all their time supervising. A working foreperson is often placed in a no-win situation by having to be counted on for actual production work vs ensuring crew members are working safely.
Conclusion
Improving anything starts with being open about where you are currently at with respect to your “Can Do vs. Make Do” culture. As leaders, you own the decision making and behaviors in the workface. It is up to you to drive improvement utilizing the suggested steps articulated above. This is difficult work, and we can help.
For assistance implementing effective SIF Prevention programs for the Utility and other high-risk industries, request a consultation.